Health and Safety
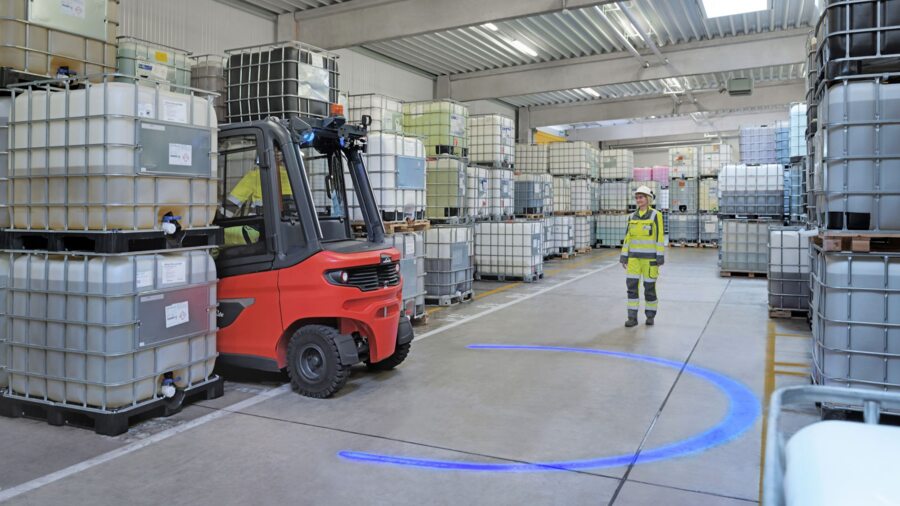
A Group-wide KION HSE standard has been in place since 2018. This standard provides the basis for uniform requirements and processes within the Group. Additional HSE regulations have been specifically set out for the legal entities as well as the sales and service companies. The regulations take into account work-specific and regional circumstances and are continuously adapted to new conditions.
At Linde MH, these Group-wide standards provide the guidelines for operational HSE implementation. Not only do these detailed regulations meet legal health and safety requirements, they often go above and beyond. This is because Linde MH always aims to ensure that its employees can do their work as safely as possible and the environmental impact is kept to a minimum.
Since 2019, the Group-wide “Golden Rules of Occupational Safety” have been helping to reduce accidents with specific instructions for managers and employees. They are communicated widely throughout the company and are proving to be successful.
Health and safety is part of the corporate strategy. This also applies to external companies that work for Linde MH. It is important that their activities are managed in such a way that the safety of the contractor’s and client’s employees, as well as visitors to Linde MH, is guaranteed and the applicable safety regulations are observed.
Health in the Workplace
Employee health is always a top priority at Linde MH, so a wide range of measures are taken to promote awareness of a healthy lifestyle. As well as providing health-related information, many sites offer preventive health checkups, dietary advice, and vegetarian dishes in the canteen. In Aschaffenburg, for example, employees can arrange a consultation with a company doctor every three years.
All Linde MH employees can access confidential in-house social counseling free of charge. This service includes solution-oriented support in overcoming crises, referrals to other institutions such as doctors, psychotherapists, counseling centers, and authorities, and face-to-face or telephone consultations.
Safety: Prevention Rather than Reaction
In accordance with the HSE standards, all workplaces at Linde MH regularly undergo a comprehensive risk assessment, from production and office spaces through to the working conditions of service technicians on customer premises. The aim is to ensure that employees come into work healthy and go home healthy—without any occupational diseases at the end of their working lives.
A site-specific HSE risk assessment was carried out for the first time in 2017. The assessment looked at the focal points of activity on site, existing facilities, and the management system in place. Based on these factors, the KION Group—including Linde MH—is classified as medium risk in terms of HSE across all industries. This one-off assessment has since evolved into an ongoing tracking process. The aim is to continuously update the risk assessment criteria and carry out high-impact assessments for new sites.
Part of this risk assessment also involves evaluating mental stress in the workplace. This is done by completing a systematic questionnaire to assess the risk to employees’ mental health due to stress, psychological fatigue, monotony, mental satiation, and emotional exhaustion and determine specific countermeasures.
2022 | 2021 | 2020 |
---|---|---|
89% | 97.8% | 100% |
Handling Working Materials and Hazardous Substances
Special care must always be taken when handling hazardous substances. An interdisciplinary hazardous substances committee therefore monitors all listed working materials along with their safety data sheets, legal aspects, and application methods, encourages their replacement with less harmful substances where necessary, defines protective measures, and is responsible for the approval of new substances.
All employees who work with a hazardous substance and all persons who may come into contact with hazardous substances are informed verbally about the hazardous substances and the correct, safe procedures for handling these substances at least once a year. This includes potential hazards, protective measures, rules of conduct, and emergency measures, and may be supplemented by practical exercises. If a health and safety hazard cannot be eliminated by technical and organizational measures, the use of personal protective equipment is required.
Emergency Management
In emergency management situations (in the event of an accident, a fire, or an unforeseeable situation), employee behavior has a decisive influence on the subsequent course of events. For this reason, Linde MH has introduced a process that ensures an appropriate, rapid, and organized response.
As well as preventing adverse effects for the company, this can have a positive impact on the public perception of the company and its relationships with customers, suppliers, investors, and employees. In this way, Linde MH creates trust and is able to use a negative situation that could affect any site and any employee to positive effect.
Up-to-date emergency plans are therefore available at all sites. These plans set out the most important information needed in an emergency in bullet point format, and are displayed in a clearly visible location, such as near the entrance or next to the fire extinguishers. Site management are responsible for preparing these plans, and are supported in this task by their safety specialists and the fire protection officers (if available).
Accidents and near-accidents are recorded and carefully analyzed at all sites using various tools. In Switzerland, for example, a special reporting app has been introduced to learn from unsafe or dangerous situations. Employees can use this app to report risk situations online so that appropriate preventive measures can be taken to prevent them arising again in the future. The reported situations and the countermeasures taken are available on the Intranet and can be viewed by all employees.
Training
Regular training and instruction in occupational health and safety ensures employees and designated individuals (e.g., first responders, fire safety officers) are able to respond quickly and appropriately in hazardous situations. All conceivable company-specific incidents and scenarios must be covered, because in the event of an accident or fire, how employees respond will have a decisive influence on the subsequent course of events.
New employees must complete workplace-specific training on the hazards relating to their activities and on protective measures and appropriate conduct in case of emergency before starting work for the first time and at least once a year thereafter. The precise nature of this training depends on the respective requirements.
Safety training includes (but is not limited to) the following topics, and is the responsibility of the respective manager:
- safety-related responsibilities of employees and managers
- conduct in an emergency (emergency call, escape routes, assembly point, etc.)
- procedure for reporting accidents in the company
- emergency contact information
- first aid and emergency equipment
- procedure and equipment in the event of fire
- general, company-specific safety precautions
- smoking and alcohol policy
- use and availability of personal protective equipment
- safe handling of hazardous substances
- safe use of machines, cranes, and forklift trucks
- the company’s environmental requirements
- potentially explosive atmospheres
- carrying out manual activities
- wellbeing and hygiene
- safe use of tools and portable electrical equipment
- safety awareness, performance incentives, and behavior-based training.
As part of the KION-wide training program for HSE specialists and managers, a comprehensive training package promoting a more proactive approach to HSE has been offered for the first time. Additional training should also be conducted as and when needed—especially after (near) accidents. Any employees who miss a training session must attend follow-up training at the earliest opportunity.
2022 | 2021 | 2020 |
---|---|---|
100% | 100% | 100% |
Field Service and Management of External Companies
Customer service employees ensure that Linde forklift trucks are always ready for use. Repair and maintenance work is often carried out directly on customers’ premises. To ensure optimal occupational health and safety for employees when working off-site too, the Service Compendium and the Linde Service Guide summarize key aspects and guidelines for safe off-site work and provide specific advice for practical implementation at the customer. Besides creating safe working conditions, they also address the ergonomic design of workplaces and service vans.
External contractors are required to inform their employees and any subcontractors about the regulations set out in Linde MH’s HSE information sheet before starting work at a Linde MH plant. Whenever there is a change in personnel, supervisors must also inform first-time employees about the specific requirements applicable to the work or construction site before starting work, then regularly thereafter and in any case at least once a year.
Occupational Health and Safety Key Figures
The key figure associated with the sustainability target of reducing the number of occupational accidents and lost time due to illness is the Lost Time Injury Frequency Rate (LTIFR1), which currently stands at 9.5 and is not expected to exceed the limit of 11 in 2023. Going forward, the aim is to reduce this limit and hence the accident frequency by at least 5% a year.
2022 | 2021 | 2020 |
---|---|---|
9.5 | 11.9 | 10.9 |
[1] Frequency of accidents with working days lost relative to one million hours worked.
2022 | 2021 | 2020 | |
---|---|---|---|
Employees incl. trainees | 208 | 255 | 190 |
Employees on a fixed-term contract | 13 | 33 | 1 |
Contractors, guests, other | 5 | 7 | 3 |
[2] Number of occupational accidents resulting in the loss of at least one working day.
Every year, the best HSE achievements of various teams from the Group’s plants around the world are assessed as part of the KION HSE Championship. Linde MH regularly comes top of the leaderboard, especially in terms of occupational safety. But more importantly, the competition has led to numerous innovative and successful safety improvements, which have then been implemented throughout the Group. Examples range from color-coded safety areas and special emergency and communication columns to driving safety training to make employees’ commute to work even safer.
2022 | 2021 | 2020 |
---|---|---|
88.2% | 89.1% | 89.7% |
Audits and Certifications
HSE certifications ensure that all relevant HSE data is available in the required quality at all times so that corrective action can be taken quickly if necessary. The assessment results also provide important points of reference for the strategic development of future activities. The KION Group’s current strategy is that all sites should be certified in accordance with ISO 45001. However, managers should be aware that this certification requires a higher standard than that specified by local legislation.
2022 | 2021 | 2020 |
---|---|---|
81.5% | 74.3% | 59.2% |
Regular HSE audits are also essential for the local organizations, as they examine the HSE management system at different intervals. These audits also ensure that all elements of the HSE system are observed on site. Internal audits are carried out regularly, on at least a quarterly basis, by a qualified individual.